Center / Hatch section
The hatch is completely framed in place. Plywood spacers are
installed and screws driven through the frames to hold everything in
alignment. The plywood is 6mm and spaced 1-2" down from the top so
that the spacers do not get glued in place. The hatch will be sawn out
once the decking is completed.
Due to the non-standard hatch and batten layout, this requires that
the plywood layer also be non-standard. Rather than have the panels meet
over a strong-back in the center, the first piece is placed over~60% of
the width, such that the longitudinal edge lands over a batten.
The engine is draped with plastic prior to gluing. |
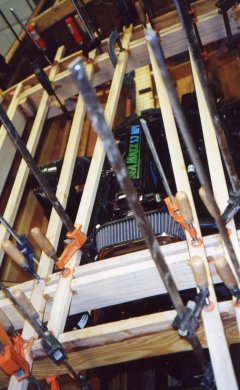 |
Plywood decking layer
The plywood (3/8" - 9mm) is laid in place and the outline is
traced from underneath with a pencil and a spacer block. The spacer
block gives a uniform lip on the plywood to allow for positioning error
as well and trimming. Cut out the pieces with a sabre saw prior to
gluing. The cut out pieces are easier to handle, leave working room in
the cockpits and conform to the deck curvature better.
The plywood is clamped and temporarily screwed in place. No more
staples! I used 3/4" dry wall screws (1" may be better).
Pre-drill the holes in the plywood after the pieces are in place. If not
predrilled, the screws will not be able to pull the plywood sown tight
and will probably strip out in the battens. Use 3-4" spacing on the
perimeter and 6" spacing along the battens. My son provides the
downward clamping force (kneeling on the deck) while drilling the holes
and screwing. He also puts the screws in the holes. It is amazing how
much quicker this is than stapling - especially during removal.
Crawl underneath and smooth the squeeze out into neat fillets. Around
the engine, pretzel shaped contortions are required, but will pay off in
easier finishing later. Pay special attention to the underside of the
hatch area. This will be visible to spectators later.
Typically, one panel (most of a 4x8' ) sheet is done at a time, which
consumes all of my clamps and allows just enough time for underside
clean-up. My schedule has been apply the deck sheet in the evening and
then remove the clamps, screws and clean up the edges first thing in the
morning. At that point the glue is set up but not yet rock hard,
allowing easier work with chisel and planes. The rabbet plane is again
most useful for edge joint clean-up. |
Here is the deck with the walnut trim "finishing boards" in
place, prior to trimming. |
Dash
The dash is a piece of curly maple that is fitted to match the
curvature of the deck. Brackets are added to give rear clearance for the
instruments as well as an ~20 degree angle to the installed dash.
Connectors are installed to allow easy removal of the dash assembly.
The view of the front of the dash shows the gauges, switches and
steering mounting plate.
The rear view of the dash shows the same plus the 4 circuit breakers.
The breakers are mounted on a piece of aluminum angle below and behind
the speedometer. The steering bracket has a back-up plate and washers to
spread the load.
The dash is installed with aluminum angle bracket on the left
rear side. It is screwed down to the center bracket with 2x #12 2"
screws underneath the steering trim cover. The right side is fastened
with an aluminum plat which is let in flush with the top of the right
bracket. No screws are visible from the front.
The dash is removed and set aside until the varnishing is
completed.
|
 |